Smith&Steward
Amateur
Hello all, my name is Matthew Tellheart, I am a semi-professional knife maker and bladesmith.
I had recently posted some knives I made up on the Flea. They were hard, sharp and straight. Fit and finish made for a pretty knife if I don't say so myself. But on the inside, there were issues with the heat treat. I would find this out later.
I had tested this design for function along with two other designs, making functional design changes here and there over the last year. After wearing and using them on a rotation basis I decided to test them further for performance.
Those tests include; a single push cut through 1/2 inch jute rope, chopping or stabbing into a block of ice, cutting a free standing price of printer paper, and finally a destructive stress test where the knife is locked in a vice, and with the assistance of a pipe I attempt to bend the knife 90° without snapping. That last test is taken from the American Bladesmith Society Journeyman Smith test.
After successful sharpness and edge retention tests I was very optimistic they would all pass the destructive stress test, they did not... After the concept pieces and prototypes for each snapped I knew there was a serious issue with the hardness of the blades. Unfortunately for me someone from the forum had responded to my post on the Flea before I could take it down. However I explained they would snap if bent too far and removed that batch of knives from sale.
I have forged and ground knives that can withstand the destructive stress test in the past, so I began a long string of destructive testing. Lining up knives from past and present to test. I now knew the problem, from a certain point on all the knives were too hard. Knowing that the times and temperatures for the heat treat process were correct that left the tempering process. Tempering is very important as it relieves the stress put on the blade during the quench.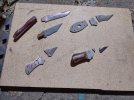
I use a separate oven for tempering. I tested this oven with three separate oven thermometer in three different places and set the oven for 350°F. After letting the oven heat up I checked the thermometers to find that the oven temp varied up to 70°F less than what read on the dial. There was the culprit, the little heat things in the oven have worn out and as a result the oven was not getting to the temperature I thought it was. All that adds up to a knife that is too hard and will snap under abusive pressure.
That may be fine for something designed and intended to be a shop or desk knife. But not for anything intended to be carried everyday, something that may be forced into a critical situation where ones life is the prize for the day.
After learning the oven temp was not in sync with the temperature dial I again placed the independent thermometers inside the oven and tried to find the right setting to get the desired temp. I eventually found the right temp setting and was ready to test a new batch of recently hardened knives. This time during the destructive test both subjects bent but still snapped... They were still too hard, they had flex but in the end came no where close to 90° during the bend. Grain structure looks nice, small and uniform just still too hard.
One option remained to me, a technique known as "Blue Backing". This is when the spine of the blade is heated with a torch very carefully to a bright blue spring temper. So tried the technique out on another knife from the batch to some success, the knife did not snap, however it did crack along the belly of the tang. So as well as blue backing I went ahead and blue bellied the rest of them...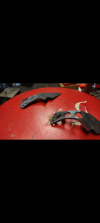
Now I am pleased with the results. The Kiridashi No.1 did fail but went pretty far for a shop knife and I did end up pushing the EDC to it's failing point which was after 90°. What remains of this batch will be finished and up on the Flea for sale in a couple weeks. The point of this sort of testing is to know without a doubt where the limit is and to know if you push past it what will happen when you do.
I have several videos of these tests on YouTube. Thank you for your time have a blessed day.
Matthew Tellheart
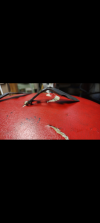
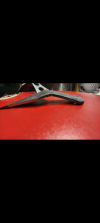
I had recently posted some knives I made up on the Flea. They were hard, sharp and straight. Fit and finish made for a pretty knife if I don't say so myself. But on the inside, there were issues with the heat treat. I would find this out later.
I had tested this design for function along with two other designs, making functional design changes here and there over the last year. After wearing and using them on a rotation basis I decided to test them further for performance.
Those tests include; a single push cut through 1/2 inch jute rope, chopping or stabbing into a block of ice, cutting a free standing price of printer paper, and finally a destructive stress test where the knife is locked in a vice, and with the assistance of a pipe I attempt to bend the knife 90° without snapping. That last test is taken from the American Bladesmith Society Journeyman Smith test.
After successful sharpness and edge retention tests I was very optimistic they would all pass the destructive stress test, they did not... After the concept pieces and prototypes for each snapped I knew there was a serious issue with the hardness of the blades. Unfortunately for me someone from the forum had responded to my post on the Flea before I could take it down. However I explained they would snap if bent too far and removed that batch of knives from sale.
I have forged and ground knives that can withstand the destructive stress test in the past, so I began a long string of destructive testing. Lining up knives from past and present to test. I now knew the problem, from a certain point on all the knives were too hard. Knowing that the times and temperatures for the heat treat process were correct that left the tempering process. Tempering is very important as it relieves the stress put on the blade during the quench.
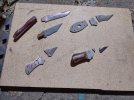
I use a separate oven for tempering. I tested this oven with three separate oven thermometer in three different places and set the oven for 350°F. After letting the oven heat up I checked the thermometers to find that the oven temp varied up to 70°F less than what read on the dial. There was the culprit, the little heat things in the oven have worn out and as a result the oven was not getting to the temperature I thought it was. All that adds up to a knife that is too hard and will snap under abusive pressure.
That may be fine for something designed and intended to be a shop or desk knife. But not for anything intended to be carried everyday, something that may be forced into a critical situation where ones life is the prize for the day.
After learning the oven temp was not in sync with the temperature dial I again placed the independent thermometers inside the oven and tried to find the right setting to get the desired temp. I eventually found the right temp setting and was ready to test a new batch of recently hardened knives. This time during the destructive test both subjects bent but still snapped... They were still too hard, they had flex but in the end came no where close to 90° during the bend. Grain structure looks nice, small and uniform just still too hard.
One option remained to me, a technique known as "Blue Backing". This is when the spine of the blade is heated with a torch very carefully to a bright blue spring temper. So tried the technique out on another knife from the batch to some success, the knife did not snap, however it did crack along the belly of the tang. So as well as blue backing I went ahead and blue bellied the rest of them...
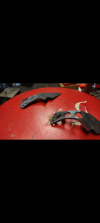
Now I am pleased with the results. The Kiridashi No.1 did fail but went pretty far for a shop knife and I did end up pushing the EDC to it's failing point which was after 90°. What remains of this batch will be finished and up on the Flea for sale in a couple weeks. The point of this sort of testing is to know without a doubt where the limit is and to know if you push past it what will happen when you do.
I have several videos of these tests on YouTube. Thank you for your time have a blessed day.
Matthew Tellheart
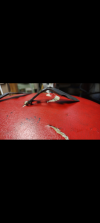
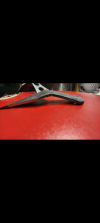